4-Spindel-Drehzentrum für Zahn-, Kegel-, Ketten- und Schalträder
Vollautomatisierte Fertigungszelle
- Simultaner Einsatz von 4 Hauptspindeln
- Vorder- und rückseitige Bearbeitung
- 4 angetriebene Werkzeuge für Bohr-, Fräsbearbeitung
- Zyklenzeit: in 60 Sekunden 2 Bauteile

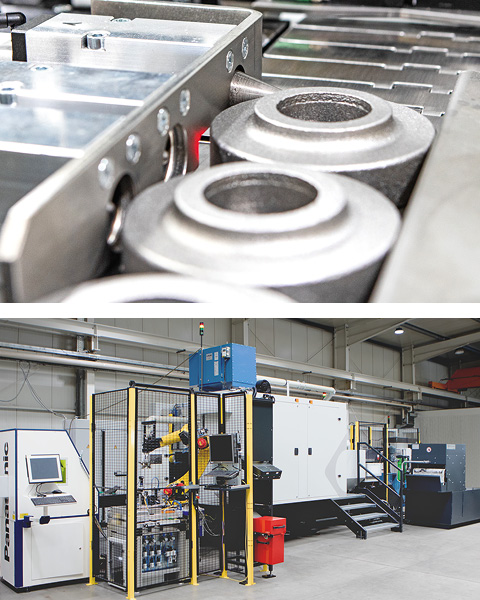
Präzision bei hoher Stückleistung und anwenderfreundlicher Bedienung
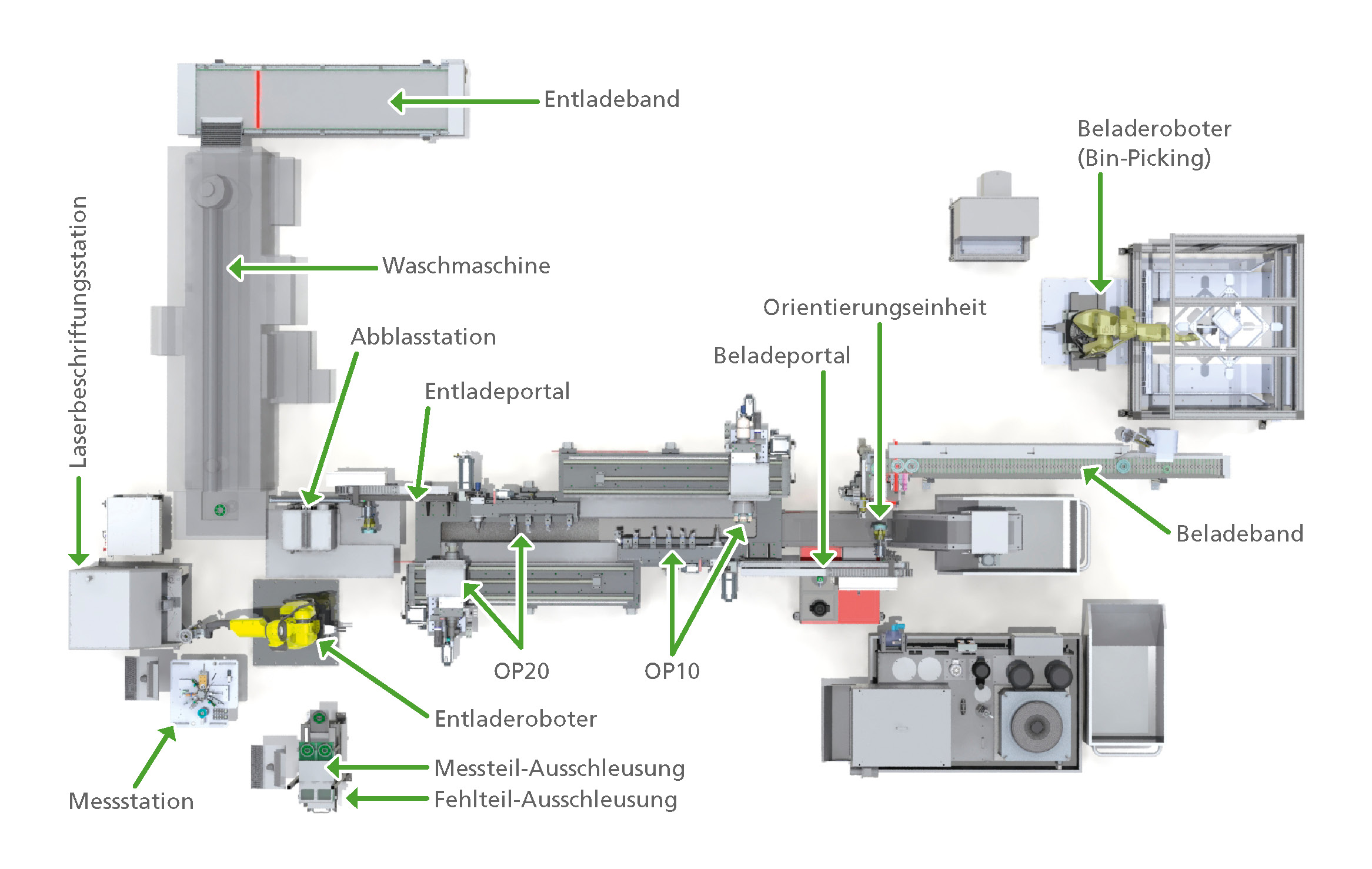
4 Spindeldrehzentrum für vorder- und rückseitige Bearbeitung von Zahn-, Kegel-, Ketten- und Schalträdern
Die geschweißte Rahmenstruktur des Flachbettes der Maschine fungiert als Tragkonstruktion für die Zerspanungseinheiten und absorbiert die entstehenden Prozesskräfte. Die Verrippungen des Bettes gewährleisten die erforderliche Steifigkeit, um eine minimale Vibration während des Zerspanungsprozesses zu gewährleisten.
Längsseitig des Bettes, in zwei Abschnitten, sind die X-Achsenführungen mit den orthogonal darauf angeordneten Z-Achsenführungen montiert. Diese Anordnung führt zu den 2 Kreuzschlitten, die die waagrechten Doppelspindeln (Synchronspindeln) tragen und positionieren. Als Absolut-Längenmesssystem sind für die Linearachsen Glasmaßstäbe eingesetzt. Die wechselseitige Anordnung der X-Achsen mit überschneidenden Fahrwegen ermöglichen den Doppelspindeln eine Bauteilübergabe in gesicherter axialer und radialer Position, somit ist die vorder- und rückseitige Bearbeitung des Werkstückes möglich. Auf 2 Ebenen, den Doppelspindeln gegenüberliegend, befinden sich die feststehenden Werkzeuge auf massiven Trägern. Die exzentrischen Lochbohrungen der Werkstücke fertigen die 4 feststehenden, angetriebenen Bohrer. Jeder Spindel ist ein angetriebenes Werkzeug zugeordnet. Das gespannte Werkstück wird über die Achsen der Spindel (X, Z und C) komplett an den feststehenden Werkzeugen bearbeitet.
Gleitführungen mit Rollentrieb zwischen den Werkzeugebenen in der X-Achse und Gleitführungen zwischen den Synchronspindeln/Doppelspindeln in Z-Achse ermöglichen die Werkzeugkorrektur verbunden mit Genauigkeiten von 0,005 mm.
Mittig zwischen den Werkzeugträgern und den X-Achsen der Doppelspindeln angeordnete Schächte leiten die fallenden Späne zum Austrag aus dem Bearbeitungsraum auf das bodennahe Förderband. Durch diese Schächte wird auch der Kühlschmierstoff zurück zur Kühlmittelanlage mit ihrem Bandfilter und den Pumpen geführt.

Vier Werkstückprogramme
- Ø 97 mm x 29 mm
- Ø 88 mm x 36 mm
- Ø 136 mm x 41 mm
- Ø 145 mm x 40 mm
Highlights
Gleichzeitige Bearbeitung von 4 Werkstücken
4 simultan arbeitende Hauptspindeln
Vorder- und rückseitige Bearbeitung
Hohe Zerspanungskräfte
Feststehende Werkzeuge für schwingungsarme Zerspanung – lange Werkzeugstandzeiten
Kurze Span- zu Spanzeit
Beladung
Die Vereinzelung der Werkstücke aus dem Schüttgut übernimmt zunächst der im Beladebereich installierte Industrieroboter im Bin-Picking Verfahren (Griff in die Kiste). In Folge werden die Schalt-/Festräder auf dem Beladeband über Stopper und pneumatischem Mitnehmer der Orientierungseinheit zur Drehlagenausrichtung zugeführt.
Der Schwenkgreifer nimmt das ausgerichtete Teil auf und führt es nacheinander den beiden übereinanderliegenden Greifer des Beladeportals zu. Die Beladung endet mit dem Fahren der Greifer zur Übergabeposition gegenüber den Doppelspindeln von OP10.
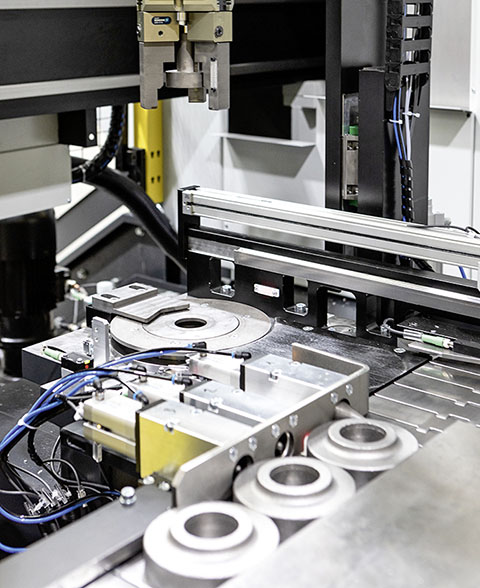
Beladeband, Stopper und pneumatischer Mitnehmer (oben), robuste Belade
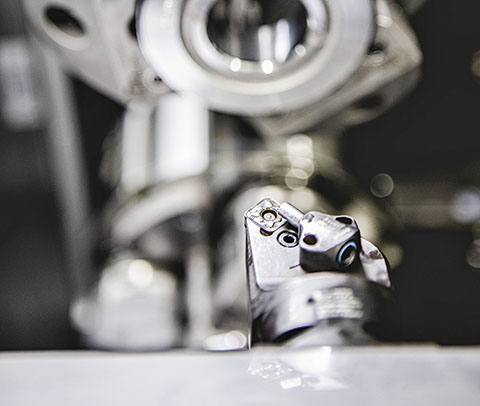
Feststehende Werkzeuge für hohe Zerspanungskräfte
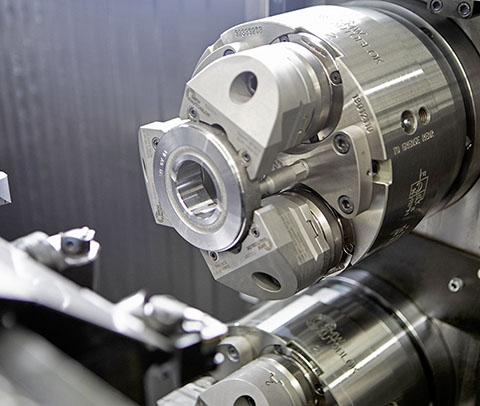
Das Werkstück fest im Griff, die Spannzange

Spanndorn mit leistungsstarker Hauptspindel
Operation 10: Mittenbohrung fertigen, Schruppen, Schlichten von Plan-, Innen- und Außenflächen
Fixiert an der Mantelaußenfläche durch die Dreibackenniederzugfutter der Doppelspindeln werden in OP 10 die beiden Schmiederohlinge vorderseitig bearbeitet:
- Bohren der Wellennabe und Herstellung der Innenpassung
- Schruppen und Schlichten von 2 radialen Planflächen mit Kontur
- Rückseitiges anfasen der Wellenpassung
- Ansenken von 7 exzentrischen Bohrungen zwischen den Stegen
- Einrollen von Beschriftung
- Drehen der verfügbaren Außenmantelteilfläche
Nach der Bearbeitung übergeben die Spindeln von OP10 im Schnittbereich beider X-Achsen die Rohlinge an die Segmentspanndorne der Doppelspindeln von OP20. Die Übergabe erfolgt in definierter axialer und radialer Lage.
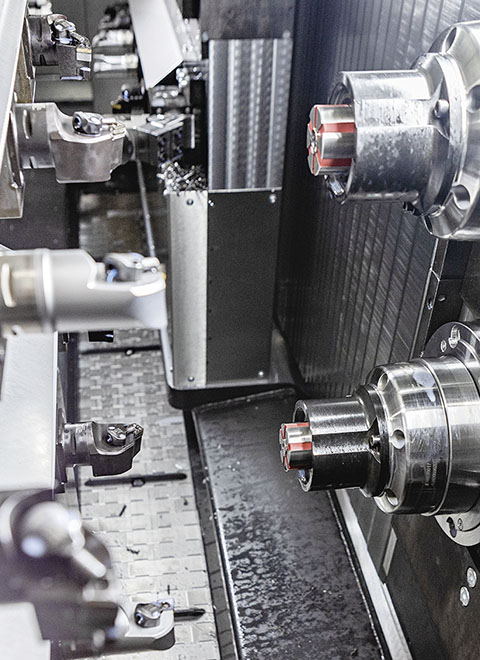
Bearbeitungsraum, übersichtlicher Werkzeugaufbau
Operation 20: Schruppen und Schlichten von Plan- und Mantelaußenfläche, Setzen von exzentrischen Bohrungen
Die Segmentspanndorne mit Anschlag – alle Spannmittel sind mit Luftanlagenkontrolle ausgestattet – halten die Werkstücke an der gefertigten Wellennabe und ermöglichen folgende rückseitige Bearbeitung:
- Schruppen und Schlichten des Außenmantels
- Schruppen und Schlichten von 2 radialen Planflächen mit Kontur
- Bohren von 7 exzentrischen Löchern zwischen den Stegen
Die Bearbeitung der Teile durch Zerspanung ist abgeschlossen, und die Segmentspanndorne werden dem Entladeportal übergeben.
Entladung: Teileabnahme, Reinigung, Qualitätssicherung, Beschriftung
Das Entladeportal entnimmt die Teile aus dem Arbeitsraum der Zerspanung und stellt sie dem Industrieroboter des Kontrollbereichs für die nachgelagerten Tätigkeiten zur Verfügung. Zur Optimierung der Verfahrwege in Verbindung mit kurzen Transportzeiten ist dieser mit einem Doppelgreifer ausgestattet.
Über die Handhabungsfunktionen des Roboters durchlaufen die Teile die Stationen:
- Abblas- und Reinigungseinheit
- Mess-, Qualitätssicherungsstation
- Messteilausschleusung für SPC-Teile, je Spindelebene getrennt
- Laserbeschriftung
- Entladeband bzw. Waschmaschine
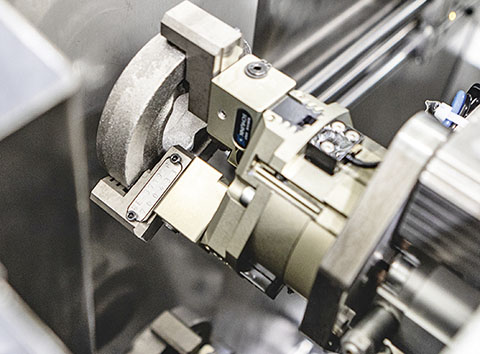
Greifer des Be-, Entladeportals
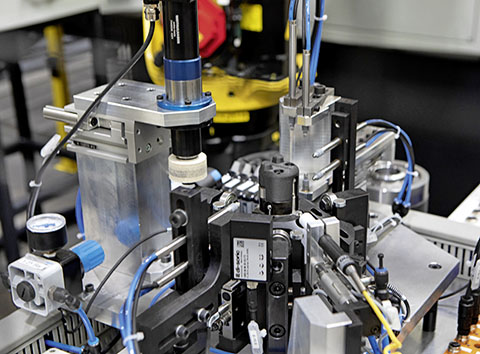
Qualitätsprüfung – Bestückung und Entnahme per Roboter

Entladeband
Serienausstattung
- 4 Arbeitsspindeln, 23,1 kW, 130 Nm, 7000 U/min, wassergekühlt
- Verfahrwege der Synchronspindeln: X: 1500 mm, Z: 240 mm
- 2 U-Achsen für Korrektur zwischen den oberen und unteren Werkzeugen
- 2 W-Achsen für Korrektur zwischen den Synchronspindeln
- 2 Spannzangen, 2 Spanndorne
- 18 feststehende Werkzeugaufnahmen Capto C4
- Prägewerkzeug OP10
- 2 angetriebene Werkzeugspindeln HSK-C 63 mit 14,6 KW, 35 Nm, 4500 U/min OP10
- 2 angetriebene Werkzeugspindeln HSK-C 63, 20,3 KW, 50 Nm, 4500 U/min OP20
- Maschinensteuerung Sinumerik 840 D SL
- Zentralschmierung
- KSS mit Kompaktbandfilter und Eintauchkühler
- Späneförderer
- Nebelabsaugung
- Hydraulikanlage
- Industrieroboter
Optionen
- Visualisierung Werkzeugverwaltung
- Bedienoberflächen
- Werkzeugbruchüberwachung
- Motorspindeln mit Drehdurchführung für Werkzeuge mit innerer Kühlschmierstoffzufuhr
Maschinenabmessung
- Werkzeugmaschine inkl. Peripherie: 15000 mm x 5000 mm
Prospekt-Download: 4-Spindel-Drehzentrum für Zahn-, Kegel-, Ketten- und Schalträder