Bearbeitungszentrum für Batterierahmen
Maximum an Flexibilität und Produktivität
- Kurze Taktzeiten durch hohe Achsenvorschubgeschwindigkeiten
- Leistungsstarke Motorspindeln für kräftige Zerspanung
- Bauteilgröße 2300 x 1500 x 500 mm
- Werkzeugspeicher für flexible Bearbeitung
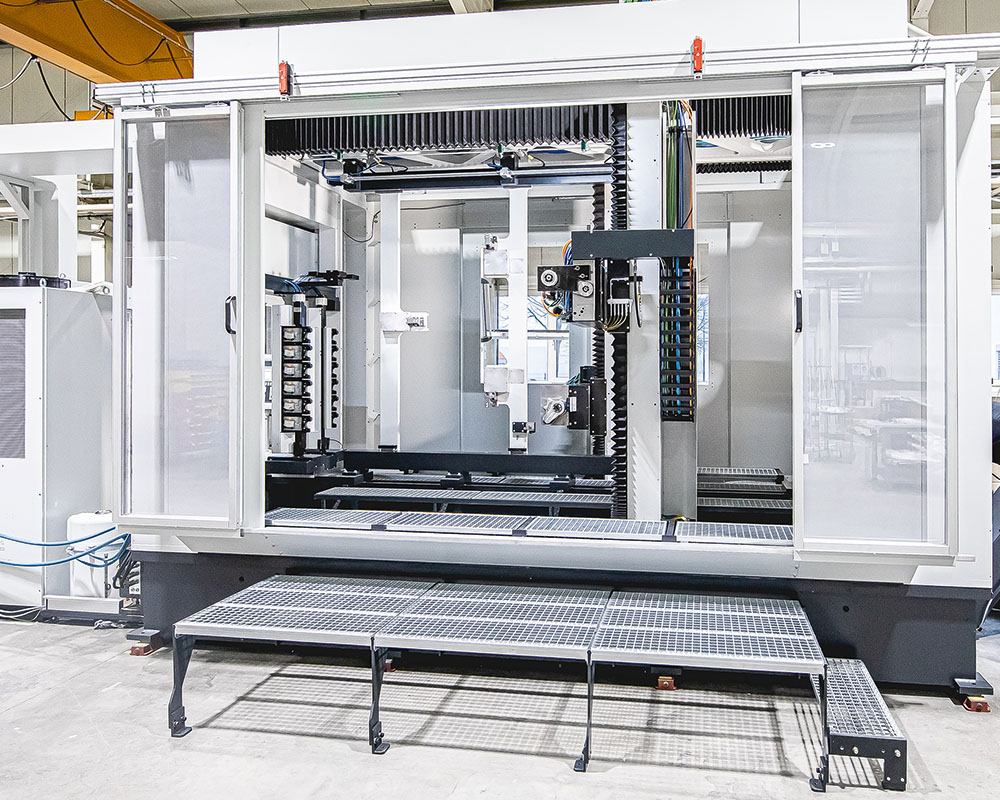
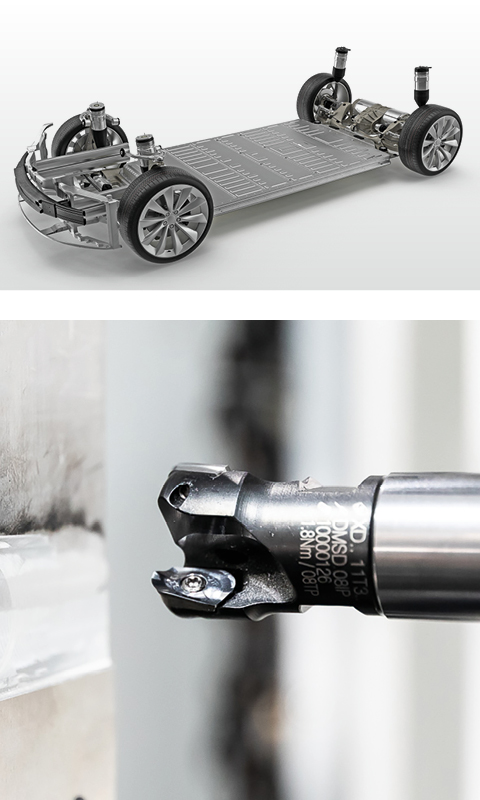
Zweiständer-Bettfräsmaschine mit senkrechtem Spannrahmen für hohen Durchsatz
Konstruiert für höchste Produktivität
Für die Bearbeitung der Batterieträger, -rahmen wird unsere Zweiständer-Bettfräsmaschine mit einem feststehenden senkrechten Spannrahmen eingesetzt. Dieser Aufbau mit den zwei sich gegenüberstehenden waagrechten Hauptspindeln, geeigneter Wahl der Werkzeuge und der Spannmittel ermöglicht eine effektive Bearbeitung an den 6 Seiten. Das Maschinenbett ist eine geschweißte Rahmenkonstruktion mit hoher Steifigkeit und hoher Stabilität.
Mit den optionalen NC-Schwenkköpfen sind sowohl auf der Vorder- wie auch auf der Rückseite des Werkstückes simultan 5 NC-Achsen verfügbar. Ergänzt durch Werkzeugspeicher (6,12 oder 24) mit der Wechseleinrichtung ist sie ein sehr flexibles, präzises Bearbeitungszentrum für alle gängigen Fertigungsverfahren: Fräsen, Bohren, Senken, Gewindeschneiden, Reiben, Schleifen, Ausspindeln.
Der Be-, Entladeroboter und die Werkstückspeicher ermöglichen dieser Fertigungszelle eine wettbewerbsfähige Herstellung von Teilen und Baugruppen in Trocken- oder Nassbearbeitung.

Weitere Anwendungen
- großformatige Gussgehäuse
- Gestelle
- Schweißkonstruktionen
- gefügte
- Rahmen- und Verkleidungsteile
- Batteriegehäuse
- Montageplatten
- Luftfahrttechnik
- Fahrwerksteile
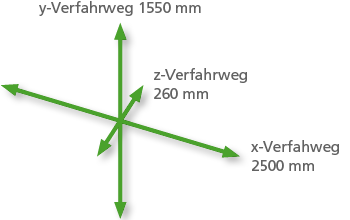
Highlights
Gleichzeitige Bearbeitung durch zwei unabhängige Frässpindeln
Großer Arbeitsraum 2500 x 1550 x 520 mm
Maximum an Flexibilität durch Werkzeugspeicher
Kürzeste Bearbeitungszeiten durch hohe Achsenvorschubgeschwindigkeiten und leistungsstarke Frässpindeln
Trocken-, Nassbearbeitung
Spanfreies Fertigteil durch integrierte Absauganlage
Wegsensor an Spindeln zur Optimierung von Bauteiltoleranzen
Hohe Prozesssicherheit durch Laserkontrolle der Werkzeuge
Automatisierte Be-, Entladung über Roboter
Erleben Sie das Bearbeitungszentrum für Batterierahmen in Aktion
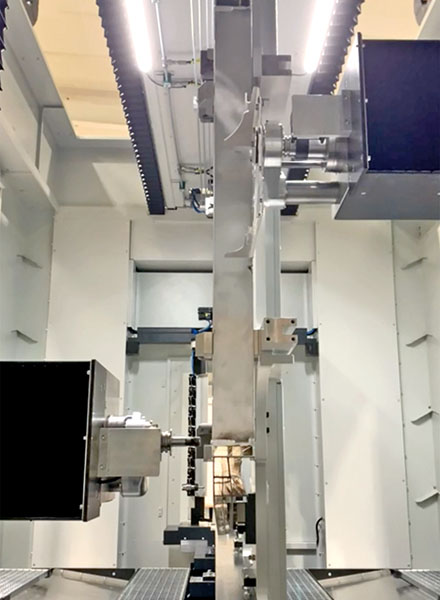
Frässpindel links und Frässpindel rechts (unter Absaugglocke) simultan an zwei Seiten im Einsatz
Be-/Entladung
Der unbearbeitete fachwerkförmige Batterieträger, bestehend aus verschweißten Aluminiumprofilen und -platten, wird vom Be-/Entladeroboter in die hydraulischen Spannelemente des Tragrahmens eingelegt und gehalten.
Gleichzeitige Bearbeitung
Der Spannrahmen fungiert als Arbeitstisch und lässt mit seiner Geometrie die 6-Seiten-Bearbeitung des Batterierahmens zu. Die Bearbeitungsaufgabe, hier das Abfräsen der Schweißnähte führen die zwei sich gegenüberstehende Motorspindeln zeitgleich aus. Jede Spindel arbeitet autark mit eigenem Werkzeugspeicher, einem laseroptischen Wegsensor und für die Prozesssicherheit mit einem Lasersystem zur Werkzeugkontrolle. Dieses detektiert Werkzeugabnutzung und -bruch vor bzw. nach der Bearbeitung.
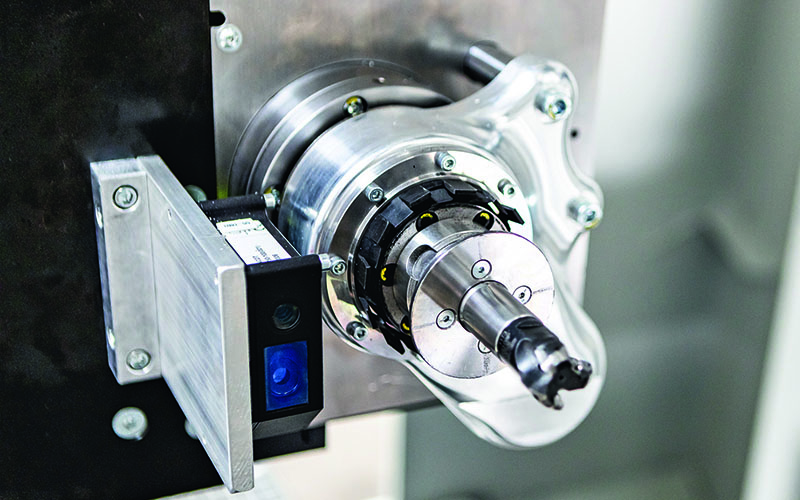
Wegsensor und Frässpindel mit eingefahrener Absaugglocke
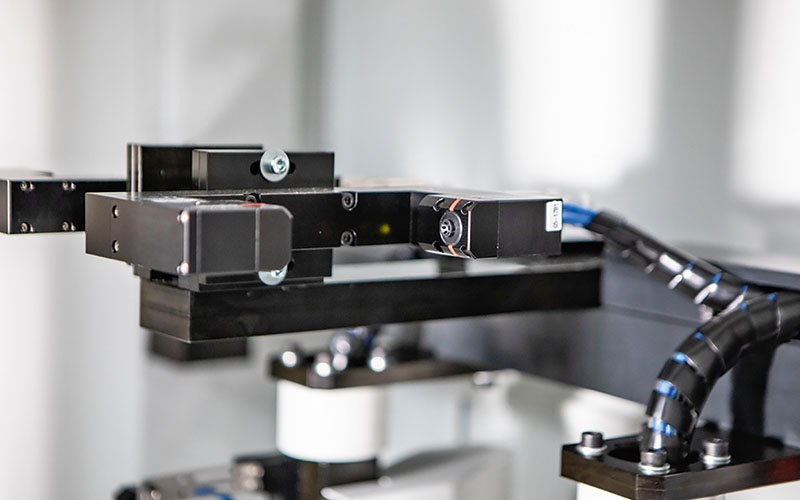
Lasersensor zur Werkzeugvermessung
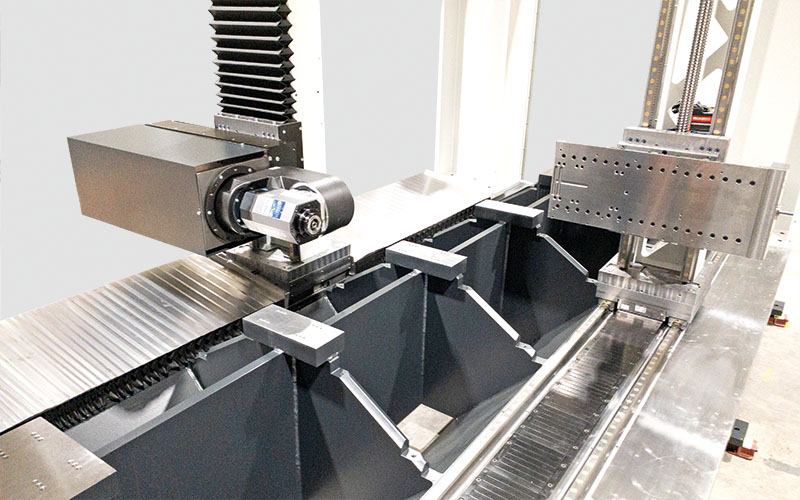
NC-Schwenkkopf und Linearantrieb x-Achse
Permanente Absaugung der Späne
Die zuschaltbare Absaugglocke, die den Fräser während der Bearbeitung umschließt und weitere Absaugschnittstellen führen zu einem spanfreien Werkstück.
Geschwindigkeit und Beschleunigung
Die x-Achse ist mit einem Linearantrieb ausgeführt.
Die Spindeleinheiten
Frässpindeldrehmoment mit HSK 50: 20 Nm im Standard.
Einmessen für 100 % Präzision
Die Herstellung der Fahrzeugbatterie erfolgt in Sandwich-Bauweise. Für die wasserdichte Ausführung müssen die Schweißnähte des Rahmenträgers auf die Ebene der Profile abgefräst werden. Somit kann in einem Folgeprozess der obere Deckel und die Schottplatte auf der späteren Fahrzeugunterseite dicht mit dem Träger verschweißt und oder verklebt werden.
Zur Sicherstellung dieser Anforderung werden die Lagetoleranzen des Schweißprozesses mit dem auf der Frässpindel angebrachten laseroptischen Längenmesssensor kompensiert. Hierzu korrigiert der Mittelwerte aus 4 Messpunkten je Bearbeitungsstelle den Fahrweg der Frässpindel individuell.
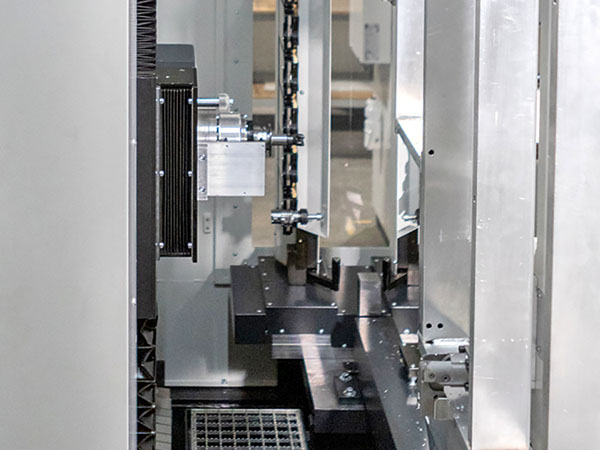
Der Arbeitsraum mit Fahrständer (links vorne), Fräskopf und Werkzeugspeicher (hinten)
Zugänglichkeit
Weit öffnende Türen und der große Arbeitsraum bieten ideale Bewegungsfreiheit für Roboter und Bedienpersonal.

Einmessung per Laser

Werkzeugwechsel
Serienausstattung
- Verfahrwege x/y/z: 2500 x 1550 x 260 mm
- Motorspindelleistung: 9,2 kW
- Spindeldrehzahl: 8000 U/min
- Drehmoment (max.): 20 Nm
- Eilgang (x/y/z): 100/30/30m/min
- Spindelkonus: HSK 50
- Werkzeugspeicher: 2 x 6 St.
- Maschinengewicht: 25.000 kg
- Steuerung: Siemens solution line 840dsl
- Späneförderer/Absaugung
Sonderausstattung
- NC-Schwenkkopf
- RFID Werkzeugkennung
- Zweiter Fräsständer links/rechts
- Zweiter Spannrahmen zur Verkürzung der Zykluszeit, Be-/Entladen bei gleichzeitigem Bearbeiten
- Drehtisch
- Werkzeugaufnahme HSK-63, HSK-80; HSK-100
- Werkzeugspeicher 12 St. oder 24 St.
Maschinenabmessung
- Werkzeugmaschine inkl. Peripherie: 7500 mm x 3100 m